The industrial machinery and components sector plays a crucial role in powering various manufacturing processes across numerous industries. As technology continues to evolve, the demand for skilled professionals who can design, develop, maintain, and optimize this machinery is on the rise. This growth translates into exciting opportunities for individuals seeking well-paying jobs in this field.
This article explores 15 of the highest-paying positions within the industrial machinery and components manufacturing landscape, along with their average salaries (according to 2023 data) and essential job duties.
1. Electrical Engineer: Commanding an Average Salary of $97,780
Electrical engineers are the backbone of the industrial machinery and components industry. They specialize in the design, development, testing, and manufacturing supervision of electrical equipment, encompassing generators, motors, radar systems, and navigation systems.
Their expertise extends across various sectors, including power generation, transmission, and distribution; building services; process control; communications; and more.
What Does an Electrical Engineer Do?
An electrical engineer’s responsibilities can vary depending on their area of specialization and employer. However, some common duties include:
- Collaborating with clients and managers to understand project requirements
- Analyzing data obtained from prototype or completed product testing
- Researching suitable solutions for specific projects
- Utilizing computer-aided design (CAD) software to create models and drawings
- Preparing reports on research findings
- Presenting findings to clients or senior management
- Overseeing technicians or junior engineers during installation or repair work
- Liaising with colleagues from other engineering disciplines on joint projects
2. Mechanical Engineer: A Rewarding Career Path at $88,430
Mechanical engineers are responsible for the design, development, and production of mechanical devices, ranging from small components to large-scale systems. Success in this career hinges on strong problem-solving skills and the ability to thrive in collaborative environments.
Duties of a Mechanical Engineer
The specific duties of a mechanical engineer can vary depending on the company and project. However, some core responsibilities include:
- Designing mechanical devices using CAD software
- Testing prototypes to ensure they meet the required specifications
- Collaborating with other engineers and professionals to finalize designs
- Overseeing the manufacturing process of products
- Evaluating product performance and implementing necessary improvements
Skills Needed to Be a Mechanical Engineer
In addition to problem-solving skills, mechanical engineers require a specific skill set to excel in their roles. These include:
- Analytical Skills: The ability to analyze data and make sound decisions based on findings, while also identifying trends and forecasting future needs.
- Communication Skills: Effective communication is vital, as mechanical engineers often collaborate with various professionals to complete projects and convey ideas to gain buy-in.
- Organizational Skills: With numerous moving parts in any given project, staying organized is essential. This involves keeping track of deadlines, budgets, and materials required.
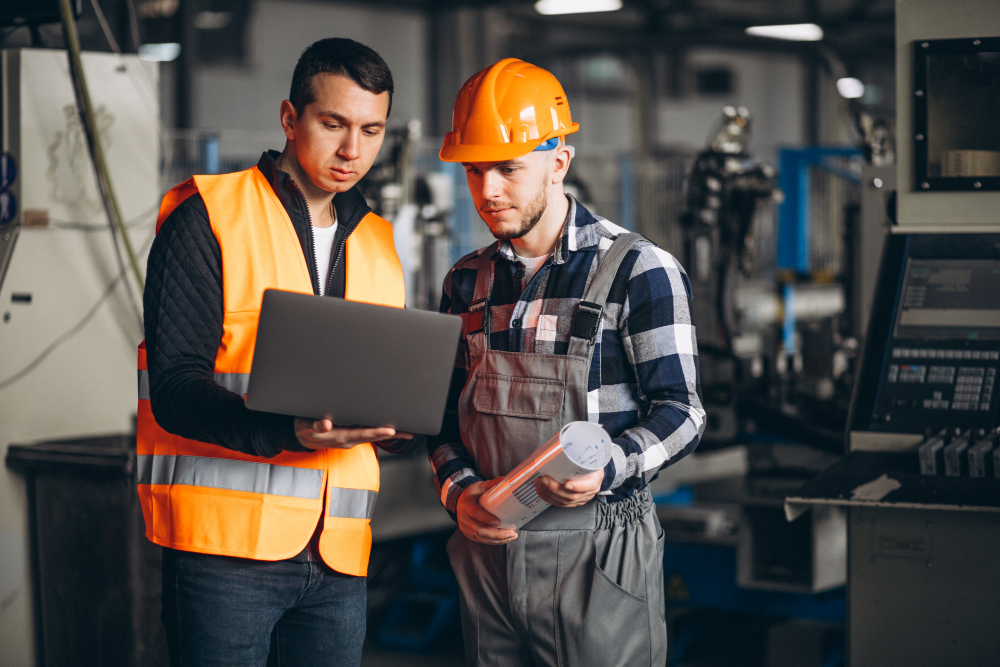
3. Industrial Engineer: Strategizing Efficiency for an Average of $87,040
Industrial engineers play a critical role in optimizing systems. Their tasks involve analyzing various systems, from manufacturing plants to patient flow in hospitals, to identify areas for improvement. By understanding how a system functions, industrial engineers pinpoint bottlenecks and inefficiencies that can be addressed.
Designing Solutions
Once areas for improvement are identified, industrial engineers design solutions to tackle these issues. This might involve anything from redesigning a factory floor layout to developing a new patient intake process. The primary goal is to find ways to make the system more efficient and effective.
Implementing Solutions
After designing a solution, the industrial engineer ensures its effective implementation. This may involve training employees on new processes or coordinating with different departments to achieve buy-in from everyone involved. The objective is to ensure the designed solution improves the system as intended.
4. Maintenance Supervisor: Overseeing Operations at $85,830
The duties of a maintenance supervisor can be categorized into three main areas: preventive maintenance, troubleshooting, and repairs.
Preventive Maintenance
A primary responsibility of a maintenance supervisor is developing and implementing a preventative maintenance plan. This plan should encompass regular inspections of all machinery and equipment, alongside routine cleaning and lubrication. By proactively identifying problems, companies can save time and money in the long run.
Troubleshooting
When a machine malfunctions, the responsibility falls on the maintenance supervisor to determine the cause of the issue and determine the solution. This may involve consulting with the machine’s operator, conducting their investigation, or ordering diagnostic tests from the manufacturer. Once the problem is diagnosed, they need to decide whether it can be fixed on-site or if the machine requires external repairs.
Repairs
In some instances, maintenance supervisors might handle repairs themselves. However, for complex problems or those requiring specialized tools or parts, they might collaborate with external vendors to get